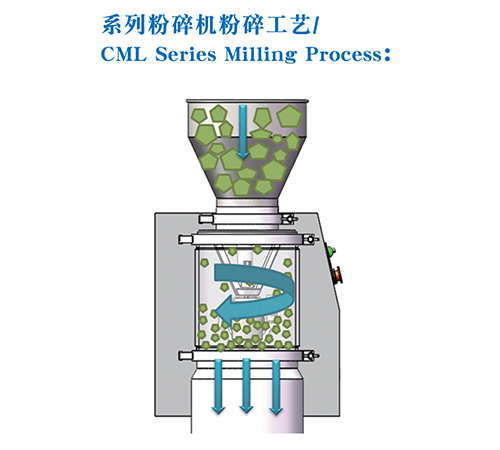
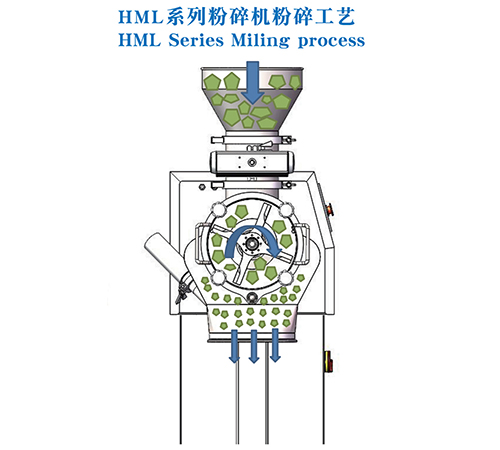
Cone Milling
Cone mills, or conical screen mills, have been used traditionally to reduce the size of pharmaceutical ingredients in a uniform manner. However, they also can be used for mixing, sieving and dispersion. They come in a variety of sizes, including tabletop laboratory devices to full-scale, high-capacity machines used for large pharmaceutical processing operations.
While the uses of cone mills vary, the trend toward using them in pharmaceuticals includes de-lumping dried materials during production; sizing wet granulated particles prior to drying; and sizing dry granulated particles after they are dried and prior to tableting.
Compared to other milling technologies, the cone mill also offers other specific advantages to pharmaceutical manufacturers. These benefits include lower noise, more uniform particle size, design flexibility and higher capacity.
The most innovative milling technology on the market today offers greater throughput and product size distribution. In addition, they are available with variable sieve (screen) and impeller options. When used with low-density materials, a sieve can increase throughput by more than 50 percent compared to mills designed with straight bars. In some cases, users have achieved unit production capacity of up to 3 tons per hour.
Achieving Dust-Free Cone Milling
It is well known that milling generates dust, which can be particularly hazardous to operators and the pharmaceutical processing environment if the dust is not contained. There are several methods available for dust containment.
Bin-to-bin milling is a fully in-line process that relies on gravity to feed ingredients through the cone mill. Technicians position a bin below the mill, and a bin placed directly above the mill releases materials into the mill. Gravity allows the material to pass directly into the bottom container after milling. This keeps the product contained from start to finish, as well as makes transferring the material easier post-milling.
Another method is vacuum transfer, which is also an in-line process. This process contains dust and also automated the process to help customers achieve higher efficiency and cost savings. Using an in-line vacuum transfer system, technicians can feed materials through the cone’s chute and have them automatically pulled from the mill’s outlet. Thus, from start to finish, the process is fully enclosed.
Finally, isolator milling is recommended to contain fine powders during milling. With this method, the cone mill integrates with an isolator through a wall fixing flange. The flange and configuration of the cone mill allow for a physical division of the cone mill head by the processing area that is outside of the isolator. This configuration allows any cleaning to be carried out inside the isolator by way of glove box. This reduces the risk of dust exposure and prevents the transfer of dust to other areas of the processing line.
Hammer Milling
Hammer mills, also called turbo mills by some pharmaceutical processing manufacturers, are typically suitable for research and product development, as well as continuous or batch production. They are often employed in cases where drug developers require precision particle reduction of difficult-to-mill APIs and other substances. In addition, hammer mills can be used to reclaim broken tablets by grinding them into powder for reforming.
For example, upon inspection, some manufactured tablets may not be up to a customer’s standards for a variety of reasons: incorrect hardness, poor appearance, and overweight or underweight. In those cases, the manufacturer can choose to mill the tablets back down to their powdered form rather than take a loss on the materials. Re-milling the tablets and introducing them back into production ultimately reduces waste and increases productivity. In almost all situations where a batch of tablets does not meet specifications, manufacturers can use a hammer mill to overcome the issue.
Hammer mills are capable of operating at speeds ranging from 1,000 rpm to 6,000 rpm while producing up to 1,500 kilograms per hour. To achieve this, some mills come equipped with an automatic rotating valve that permits technicians to fill the milling chamber evenly with ingredients without overfilling. Besides preventing overfill, such automatic feeding devices can control the flow of powder into the milling chamber to increase process repeatability and reduce heat generation.
Some of the more advanced hammer mills have a dual-sided blade assembly that increases the viability of wet or dry ingredients. One side of the blade acts as a hammer to shatter dry materials, while a knife-like side can slice through wet ingredients. Users simply flip the rotor based on the ingredients they are milling. Additionally, some mill rotor assemblies can be reversed to adjust for specific product behavior while the rotation of the mill remains unchanged.
For some hammer mills, particle size is determined based on the screen size that is chosen for the mill. Modern hammer mills can reduce material size to as small as 0.2 mm to 3 mm. Once processing is complete, the mill pushes particles through the screen, which regulates the product size. The blade and screen perform in conjunction to determine the final product size.
Post time: Aug-08-2022